The difference between automatic dimming welding lenses and ordinary lenses
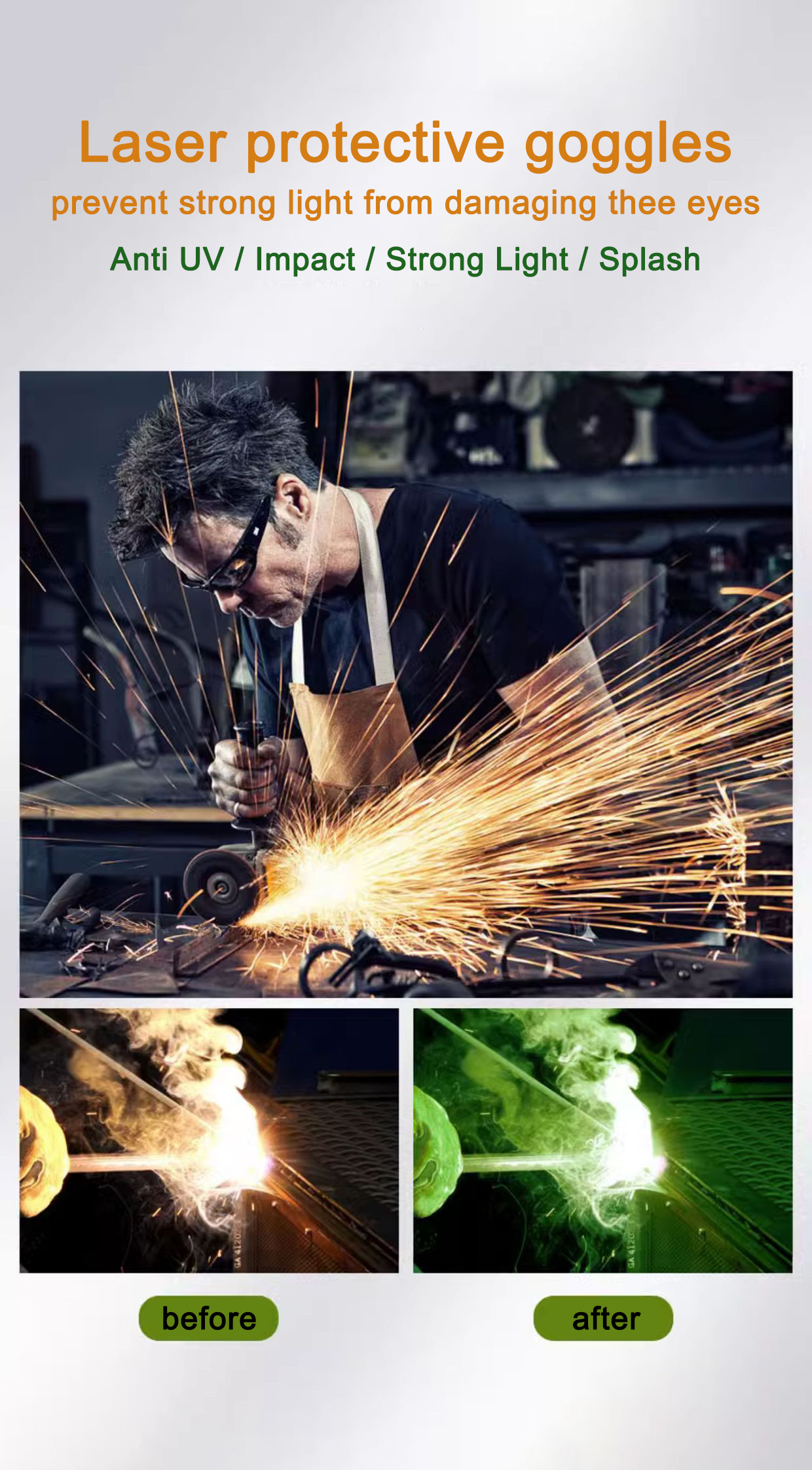
Five key points you need to know
# Different uses
Automatic dimming welding lenses are a special type of glasses mainly used to protect the eyes of welders from strong light radiation, while also providing the necessary light for welding. Ordinary glasses are used for correcting vision and protecting the eyes, but cannot provide the necessary light for welding.
# Different filling materials
Automatic dimming welding lenses usually use liquid crystal filling materials, which can automatically change color or isolate light according to the intensity of the received light. Ordinary glasses, on the other hand, use vision correction or transparent materials.
# Different reaction times
The automatic dimming welding lens has a fast reaction speed, allowing welders to quickly adapt to the conversion of strong and weak light, thereby improving work efficiency. Ordinary glasses do not have automatic dimming function.
# Different prices
The price of automatic dimming welding lenses is relatively high. Compared to ordinary glasses, the application of LCD technology and light sensing technology makes automatic dimming welding lenses more precise and durable.
# Different usage scenarios
Automatic dimming welding lenses are mainly used in industrial manufacturing and welding work, such as in fields such as ships and mechanical equipment. Ordinary glasses are suitable for daily use. Overall, there are many significant differences between automatic dimming welding lenses and regular glasses.
What kind of people will use welding goggles?
In summary, welding goggles and regular glasses have distinct differences in their purpose and design. Welding goggles focus on providing safety protection, while regular glasses are primarily for vision correction and aesthetics.
Welding goggles and regular glasses differ in several key aspects, mainly in terms of function, design, and materials. Here are the primary differences between the two:
1.Function:
1-1.Welding Goggles: These are primarily used to protect the eyes from the intense light, ultraviolet (UV) rays, infrared (IR) radiation, and flying metal debris generated during welding. They offer protective functions to block harmful light and physical damage.
1-2.Regular Glasses: These are mainly used to correct vision problems (such as myopia, hyperopia, astigmatism) or as fashion accessories. Regular glasses do not have protective functions against intense light or harmful radiation.
2.Lens Materials:
2-1.Welding Goggles: The lenses are typically made from special protective materials that can filter out harmful UV and IR rays and have high impact resistance.
2-2.Regular Glasses: The lenses are usually made from optical glass or plastic, primarily to provide clear vision without special protective features.
3.Lens Color:
3-1.Welding Goggles: The lenses are usually dark or tinted to filter out the intense light produced during welding. This tint significantly reduces light intensity to protect the eyes.
3-2.Regular Glasses: The lenses are typically clear unless they are sunglasses or photochromic lenses designed to protect eyes in sunlight.
4.Design and Structure:
4-1.Welding Goggles: These are designed to be more robust, often covering a larger area with side shields to prevent flying debris from entering the eyes. Some welding goggles also come with adjustable headbands to ensure they stay secure during work.
4-2.Regular Glasses: These are designed to be lightweight, focusing on comfort and aesthetics. The frame materials vary, including metal, plastic, and composites, but generally lack protective features.
5.Applicable Situations:
5-1.Welding Goggles: Suitable for welding, metal cutting, grinding, and other industrial or manufacturing environments that require eye protection.
5-2.Regular Glasses: Suitable for everyday life, work, and study, used for vision correction or fashion purposes.
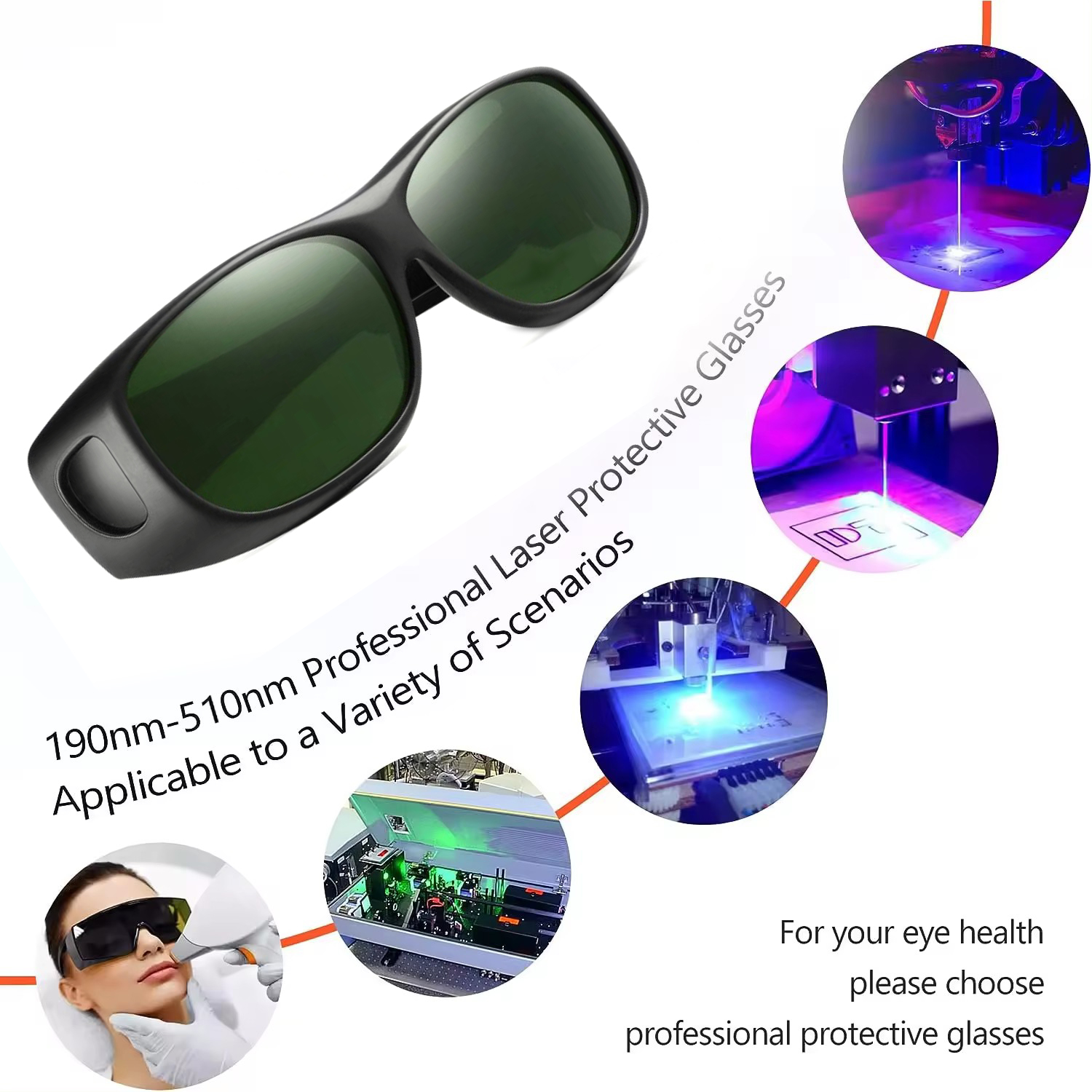
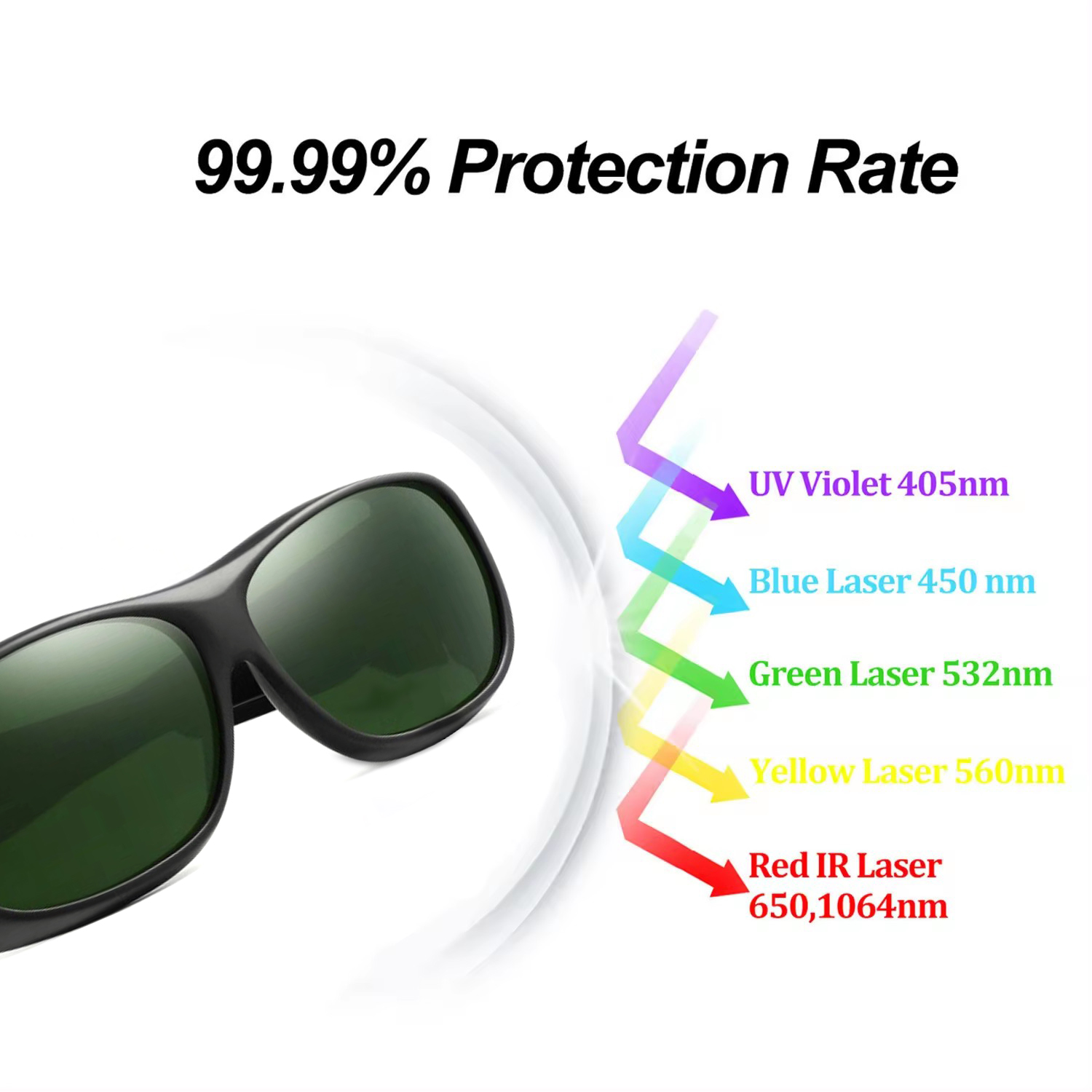
Welding goggles are mainly used to protect the eyes of welders and other personnel involved in welding work. The following are some people who will use welding glasses:
1.Welders: This is the main user group who need to protect their eyes from strong light, splashing metal fragments, and harmful radiation during welding operations.
2.Metal workers: In addition to welders, other workers engaged in metal processing may also need to use welding goggles, such as those who cut, grind, and polish metal.
3.Manufacturing workers: In some manufacturing industries, workers involved in welding and metal processing will use welding goggles to protect their eyes.
4.Construction workers: On construction sites, welding and metal cutting also require the use of welding goggles.
5.Repair worker: Engaged in repair and maintenance work, especially workers involved in welding and cutting, also use welding goggles.
6.Car repairman: During the car repair process, welding and cutting metal parts also require welding glasses to protect the eyes.
7.DIY enthusiasts and amateur welders: Some enthusiasts who enjoy hands-on metal processing or welding also use welding goggles to protect themselves.
Welding goggles can effectively prevent the harm of strong light and harmful radiation to the eyes, and are essential safety equipment in these working environments.
Why does welding damage your eyes?
Welding can damage your eyes due to several harmful factors associated with the welding process:
# Intense Light and Ultraviolet (UV) Radiation:
##Arc Eye (Photokeratitis): Exposure to the intense light produced during welding, particularly ultraviolet (UV) radiation, can cause a condition known as "arc eye" or photokeratitis. This is akin to a sunburn on the surface of the eye, resulting in pain, redness, tearing, and a feeling of grit or sand in the eye.
##Cataracts: Prolonged exposure to UV radiation from welding can contribute to the development of cataracts, a condition where the lens of the eye becomes cloudy, leading to impaired vision.
# Infrared (IR) Radiation:
##Prolonged exposure to infrared radiation emitted during welding can damage the retina, the light-sensitive layer at the back of the eye, potentially leading to vision loss.
# Visible Light:
##The bright visible light produced by welding can cause temporary blindness or "welders' flash," a condition where the eyes are overwhelmed by bright light, leading to temporary vision impairment.
# Flying Debris and Particles:
##During welding, sparks, metal fragments, and other debris can fly into the air and potentially enter the eyes, causing physical injuries such as cuts, abrasions, or even penetrating injuries to the eye.
# Chemical Fumes and Vapors:
##Welding can produce harmful fumes and vapors that may irritate the eyes and respiratory system. Prolonged exposure to these fumes can cause chronic eye irritation and other health issues.
To prevent eye damage, welders must wear appropriate protective gear, including welding goggles or helmets with the proper shade of filter lenses to block harmful UV and IR radiation, and safety shields to protect against flying debris. Additionally, ensuring proper ventilation can help minimize exposure to harmful fumes and vapors.
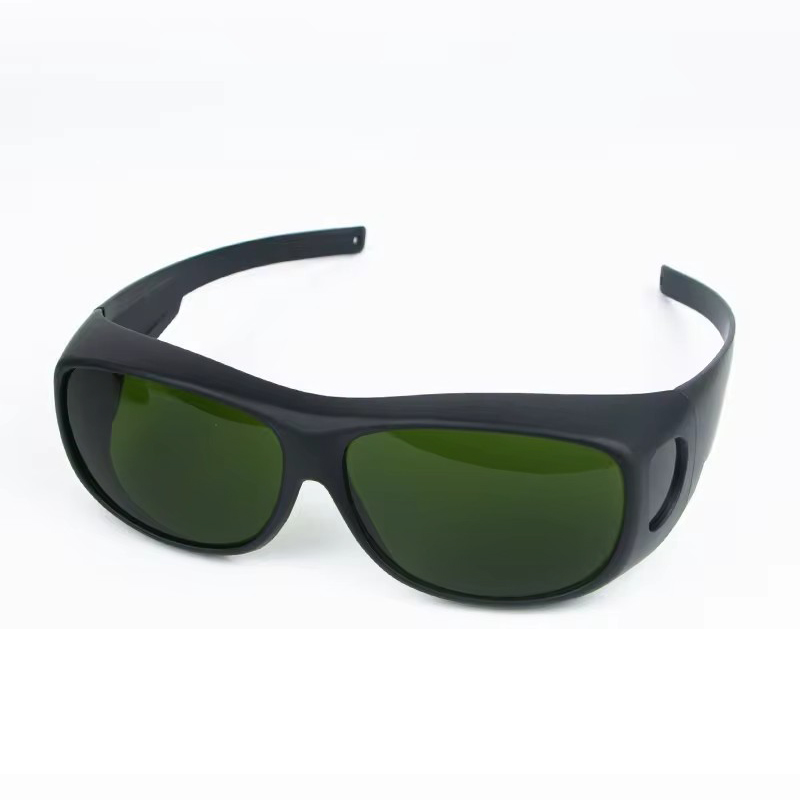
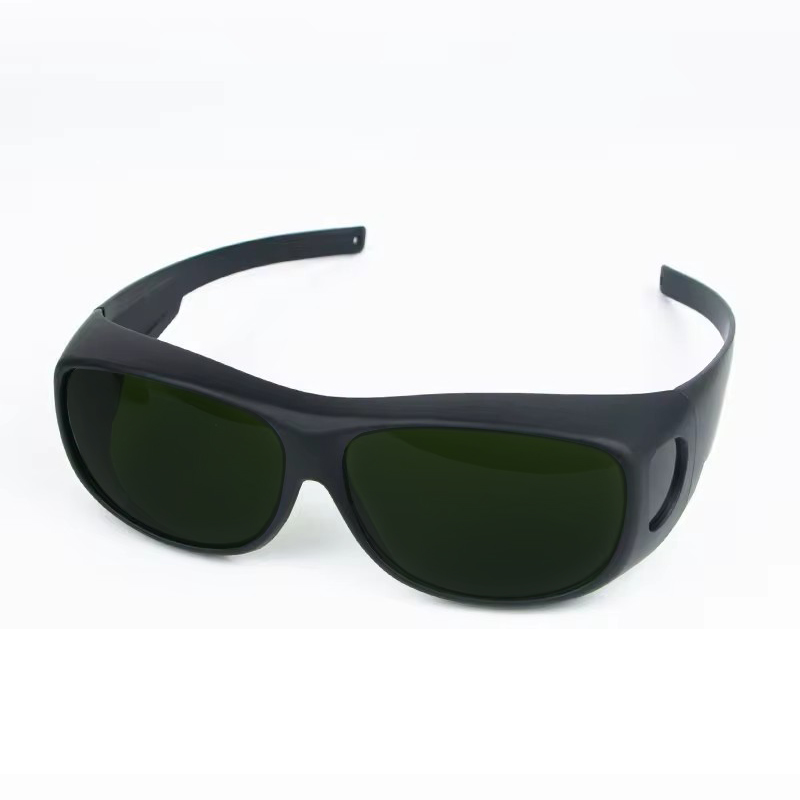
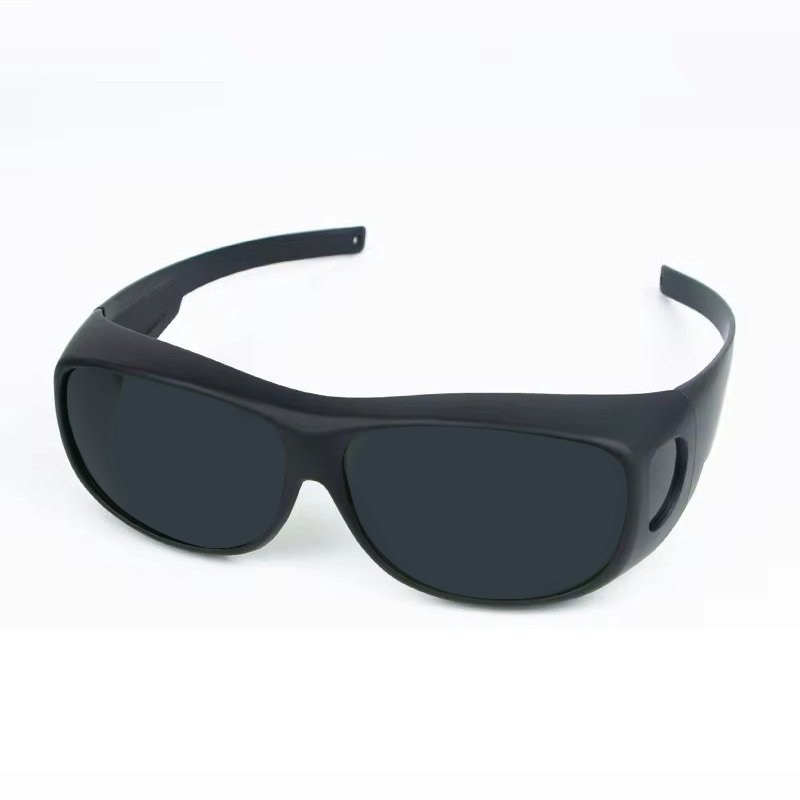
Which safety glasses are the best?
Choosing the best safety glasses depends on the specific requirements of your work environment and personal needs. However, some key features and considerations can help you identify high-quality safety glasses:
#Certification and Standards:
##Look for safety glasses that meet or exceed industry standards such as ANSI Z87.1 (American National Standards Institute) or EN166 (European Standard). These certifications ensure the glasses provide adequate protection against impact, radiation, and other hazards.
#Lens Material:
##Polycarbonate lenses are commonly used in safety glasses due to their high impact resistance, lightweight nature, and inherent UV protection.
##Trivex lenses offer similar benefits but with better optical clarity and scratch resistance.
#Lens Coatings:
##Anti-Fog Coating: Prevents the lenses from fogging up, especially in environments with varying temperatures.
##Anti-Scratch Coating: Extends the life of the lenses by protecting them from scratches.
##UV Protection: Essential for outdoor work or environments with UV exposure.
#Frame Design:
##Look for wraparound frames or side shields to provide additional protection from debris and particles entering from the sides.
##Adjustable frames or temples can ensure a better fit and comfort for prolonged use.
#Comfort and Fit:
##Ensure the safety glasses are comfortable to wear for extended periods. Features such as adjustable nose pads, cushioned temples, and lightweight materials contribute to comfort.
##Some safety glasses are designed to fit over prescription glasses (OTG - Over The Glasses) for those who need vision correction.
Specific Use Cases:
1.For welding, safety glasses with the appropriate shade of filter lens (usually marked with a shade number) are necessary to protect against intense light and radiation.
2.For chemical handling, splash-resistant goggles may be more suitable than standard safety glasses.
How do welding glasses work?
Welding glasses, also known as welding goggles, work by protecting the eyes from the harmful effects associated with welding processes. Here’s how they accomplish this:
1.Filtering Harmful Radiation:
1-1.Ultraviolet (UV) Radiation: Welding glasses have special lenses that block or filter out harmful UV radiation produced during welding. UV radiation can cause serious eye injuries such as photokeratitis (arc eye).
1-2.Infrared (IR) Radiation: The lenses also block IR radiation, which can penetrate deep into the eye and potentially damage the retina, leading to long-term vision problems.
2.Reducing Intense Visible Light:
2-1.Welding produces an extremely bright light, which can be blinding and cause temporary or permanent vision damage. Welding glasses use dark or tinted lenses to reduce the intensity of this visible light to safe levels, protecting the eyes from flash blindness and welder’s flash (a condition similar to sunburn on the cornea).
3.Physical Protection:
3-1.Impact Resistance: Welding glasses are made from materials like polycarbonate that are highly impact-resistant. This protects the eyes from flying debris, sparks, and metal fragments that are common in welding environments.
3-2.Side Shields: Many welding glasses come with side shields or a wraparound design to provide additional protection from particles entering the eyes from the sides.
4.Comfort and Fit:
4-1.Welding glasses are designed to fit securely on the face, often with adjustable features such as elastic straps, nose pads, and temple arms. This ensures that the glasses stay in place and provide consistent protection throughout the welding process.
5.Shade Numbers:
Welding glasses come with different shade numbers, indicating the level of darkness and the amount of light they filter. The appropriate shade number depends on the type of welding and the intensity of the light. Higher shade numbers provide darker lenses and are used for more intense welding processes like arc welding, while lower shade numbers are used for less intense processes like torch soldering
Key Components of Welding Glasses
#Lens Material:
##Typically made from polycarbonate or other high-impact materials, the lenses are designed to be durable and resistant to both impact and high temperatures.
#Coatings:
##Anti-fog Coating: Prevents the lenses from fogging up, which is crucial in environments with varying temperatures or when the user is sweating.
##Anti-scratch Coating: Enhances the durability of the lenses by protecting them from scratches, ensuring clear vision.
#Frame:
##The frame is designed to be robust and often includes side shields or a wraparound design to provide comprehensive protection. It should fit comfortably and securely to prevent slipping during use.
#Summary
##In essence, welding glasses protect the eyes by filtering out harmful UV and IR radiation, reducing the intensity of visible light, and providing physical protection from debris and sparks. The combination of specialized lens materials, coatings, and a secure fit ensures that welders can work safely without risking damage to their eyes.
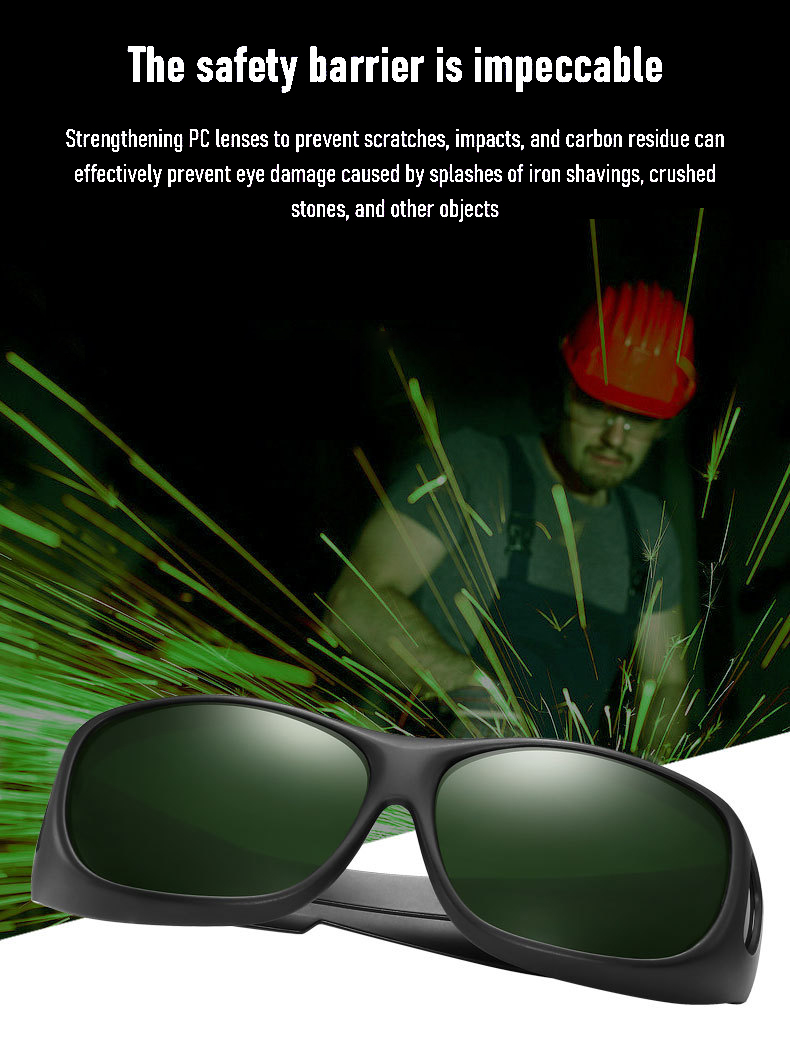
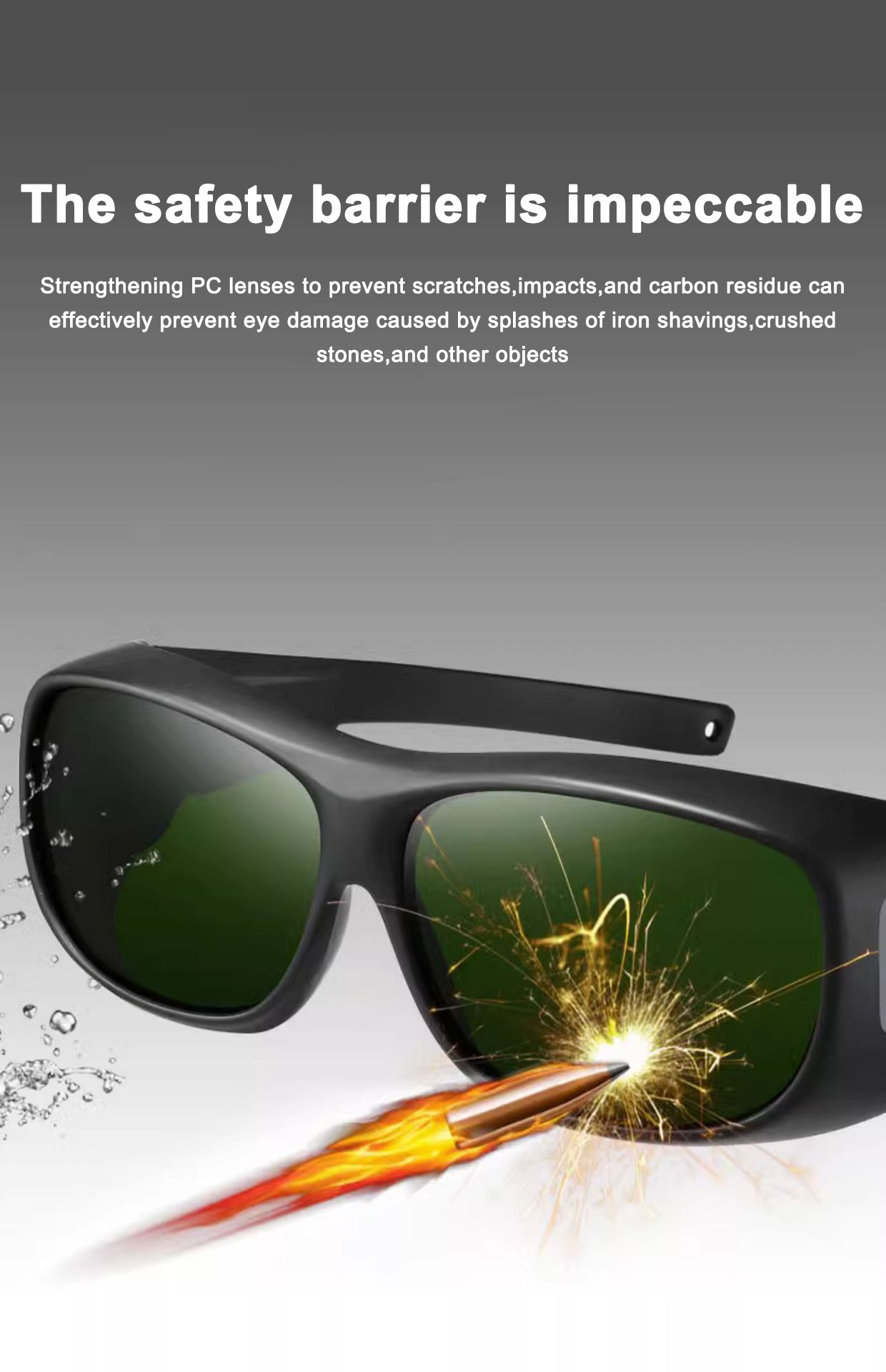
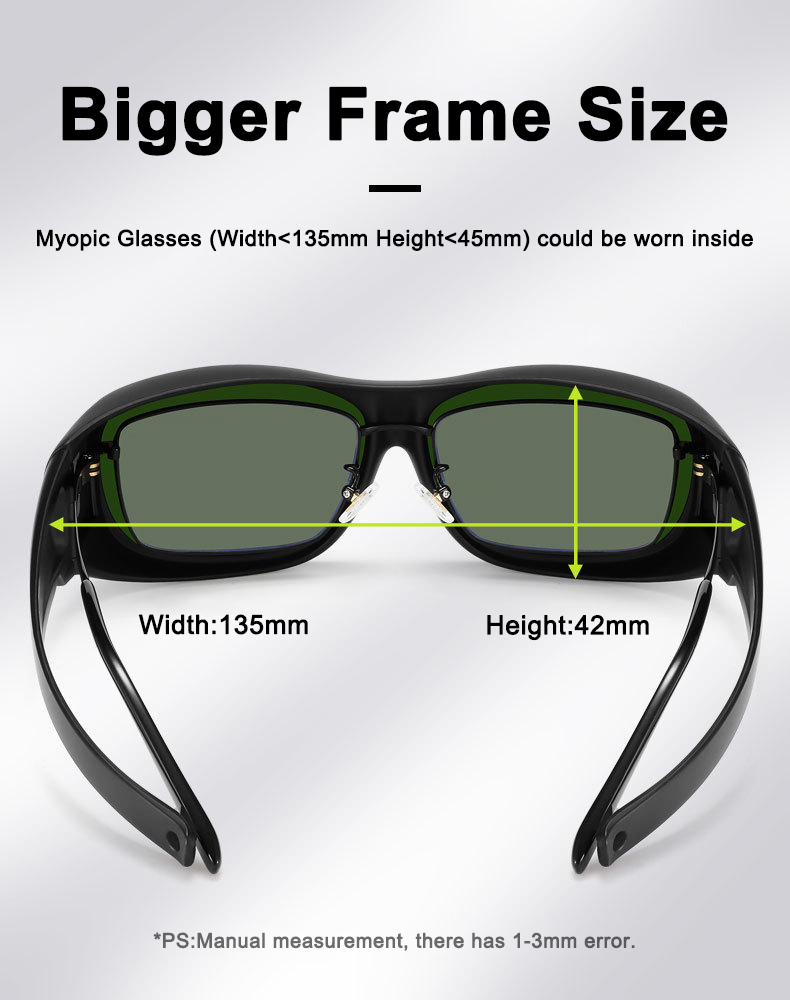
Why are welding glasses green?
Welding glasses are typically green because the green lenses are effective in filtering out harmful radiation while allowing welders to see their work clearly. Here’s a detailed explanation of why green lenses are commonly used:
1.Filtering Harmful Radiation
1-1.Ultraviolet (UV) Radiation:
1-1-1.Welding processes produce significant amounts of UV radiation, which can cause serious eye injuries such as photokeratitis (arc eye). Green lenses effectively filter out UV radiation, protecting the welder’s eyes from these harmful rays.
1-2.Infrared (IR) Radiation:
1-2-1.Welding also generates IR radiation, which can penetrate deep into the eye and damage the retina. Green lenses block a significant portion of IR radiation, reducing the risk of long-term eye damage.
1-3.Visible Light:
1-3-1.Welding emits very bright visible light, which can cause flash blindness and other temporary vision problems. Green lenses reduce the intensity of visible light to safe levels, allowing welders to work without being blinded by the brightness.
2.Enhancing Visibility and Comfort
2-1.Contrast and Clarity:
2-1-1.The green tint enhances contrast and clarity, making it easier for welders to see the weld puddle and surrounding work area. This improved visibility is crucial for precise welding.
2-2.Reducing Eye Strain:
2-2-1.Green lenses help reduce eye strain by minimizing glare and bright reflections. This is especially important during long welding sessions, as it helps prevent fatigue and discomfort.
3.Practical Considerations
3-1.Material and Coatings:
3-1-1.The lenses in welding glasses are often made from polycarbonate or other impact-resistant materials, with a green tint applied either as a coating or integrated into the lens material itself. This ensures durability and consistent protection.
3-2.Color Perception:
3-2-1.While green lenses filter out specific wavelengths of light, they still allow welders to perceive colors accurately. This is important for tasks that require color differentiation, such as inspecting welds or identifying materials.
Summary
In summary, welding glasses are green because the green tint is highly effective at filtering out harmful UV and IR radiation, reducing the intensity of visible light, and enhancing visibility and comfort for welders. The green lenses provide the necessary protection and visual clarity needed for safe and precise welding operations.
Will safety glasses hurt my eyes?
Safety glasses are designed to protect your eyes and should not cause harm if they are used correctly. However, there are some factors to consider to ensure they are comfortable and safe to use:
Factors to Ensure Safety Glasses Do Not Hurt Your Eyes
1.Proper Fit:
1-1.Ensure the safety glasses fit well. They should sit comfortably on the bridge of your nose and rest securely on your ears without causing pressure points.
1-2.Adjustable frames and temples can help achieve a better fit, reducing discomfort during prolonged use.
2.Lens Quality:
2-1.High-quality lenses are essential. Poorly made lenses can cause visual distortions, leading to eye strain or headaches.
2-2.Look for lenses that meet safety standards like ANSI Z87.1 or equivalent, ensuring they provide adequate protection and optical clarity.
3.Anti-Fog and Anti-Scratch Coatings:
3-1.Anti-fog coatings can prevent lenses from fogging up, which can be particularly helpful in environments with temperature fluctuations.
3-2.Anti-scratch coatings help maintain clear vision by reducing scratches that can obscure your view.
4.Weight and Material:
4-1.Lightweight materials, such as polycarbonate, can enhance comfort by reducing the pressure on your nose and ears.
4-2.Ensure the materials are hypoallergenic, especially if you have sensitive skin or allergies.
5.Ventilation:
5-1.Good ventilation can help prevent fogging and keep your eyes comfortable. Some safety glasses come with ventilation features to improve airflow.
6.Regular Breaks:
6-1.If you are wearing safety glasses for extended periods, take regular breaks to rest your eyes. This can help reduce eye fatigue and discomfort.
Potential Issues and Solutions
#Pressure Points:
##If the glasses are causing pressure on certain areas, try adjusting the fit or switching to a different style that distributes pressure more evenly.
#Lens Distortion:
##Poor quality or damaged lenses can cause visual distortions. Replace any scratched or damaged lenses and ensure the glasses you choose are of high optical quality.
#Allergic Reactions:
##Some materials might cause skin irritation or allergic reactions. If this happens, look for safety glasses made from hypoallergenic materials.
#Inadequate Protection:
##Ensure the safety glasses provide the necessary level of protection for your specific tasks. Inadequate protection can lead to accidents and eye injuries.
#Conclusion
##Safety glasses should not hurt your eyes if they are of good quality, fit properly, and are suited to the specific hazards of your work environment. By choosing the right pair and ensuring they are comfortable and well-maintained, you can protect your eyes effectively without discomfort.
How safety glasses are made?
Safety glasses are made through a series of carefully controlled manufacturing processes to ensure they meet safety standards and provide adequate protection. Here’s an overview of the key steps involved in making safety glasses:
1. Design and Specifications1.
1-1.Standards and Requirements: Safety glasses must meet specific standards such as ANSI Z87.1, EN166, or other relevant regulations. These standards dictate the design, materials, and performance criteria.
1-2.Design Process: Engineers and designers create models and prototypes using computer-aided design (CAD) software, focusing on factors like fit, comfort, and protection.
2. Material Selection2.
2-1.Lens Material: The most common materials for safety lenses are polycarbonate and Trivex, known for their high impact resistance, lightweight nature, and clarity.
2-2.Frame Material: Frames are typically made from durable, lightweight materials like polycarbonate, nylon, or metal alloys.
3. Lens Manufacturing3.
3-1.Injection Molding: Polycarbonate or Trivex pellets are melted and injected into molds to form lenses. This process ensures that the lenses are durable and impact-resistant.
3-2.Casting and Curing: For some materials, liquid monomers are cast into molds and then cured under heat and pressure to form solid lenses.
4. Lens Coating and Treatment4.
4-1.Anti-Scratch Coating: Lenses are coated with a hard layer to protect against scratches and extend their lifespan.
4-2.Anti-Fog Coating: A chemical treatment is applied to prevent condensation from forming on the lenses.
4-3.UV Protection: Lenses may be treated or inherently block UV radiation to protect the eyes from harmful rays.
5. Frame Manufacturing
5-1.Injection Molding: Similar to lens manufacturing, frame components are often produced through injection molding to create precise and durable parts.
5-2.Assembly: Frame components are assembled, including hinges, nose pads, and temples. Adjustability features like flexible arms or adjustable nose pieces may be added for comfort.
6. Quality Control and Testing6.
6-1.Impact Testing: Safety glasses undergo rigorous impact testing to ensure they can withstand high-velocity impacts without breaking.
6-2.Optical Clarity: Lenses are tested for optical clarity to ensure they do not distort vision.
6-3.Fit and Comfort Testing: Frames are evaluated for fit and comfort, ensuring they stay securely on the face without causing discomfort.
7. Final Assembly
7-1.Lens Insertion: Lenses are inserted into the frames. This process may involve snapping the lenses into place or securing them with screws.
7-2.Final Inspection: Each pair of safety glasses undergoes a final inspection to check for defects, proper assembly, and adherence to quality standards.
8. Packaging and Distribution8.
8-1.Packaging: Safety glasses are packaged with appropriate instructions and safety information. Packaging is designed to protect the glasses during shipping and handling.
8-2.Distribution: The finished safety glasses are distributed to retailers, distributors, or directly to consumers.
Summary
The manufacturing process for safety glasses involves careful design, material selection, precise molding and coating techniques, rigorous testing, and thorough quality control to ensure they provide effective protection and comfort. By adhering to strict standards and utilizing advanced manufacturing techniques, manufacturers produce safety glasses that are reliable and safe for use in various hazardous environments.
When to Replace Safety Glasses?
1.Visible Damage:
1-1.Scratched Lenses: If the lenses are scratched, it can impair vision and reduce the effectiveness of the protective coatings. Replace the glasses if scratches are noticeable and affect visibility.
1-2.Cracked or Broken Frames: Any cracks or breaks in the frames compromise the structural integrity and protection of the glasses. Replace immediately if you notice any damage.
2.Lens Coating Wear:
2-1.Worn or Peeling Coatings: Anti-scratch, anti-fog, or UV protection coatings can wear off over time. If you notice peeling or reduced effectiveness of these coatings, it’s time to replace the glasses.
3.Fit and Comfort Issues:
3-1.Loose or Damaged Parts: Adjustable parts like nose pads, temple arms, or headbands that become loose or damaged can affect the fit and protection of the glasses. Replace if these parts no longer provide a secure and comfortable fit.
4.Exposure to Harsh Conditions:
4-1.Chemical Exposure: If the glasses have been exposed to harsh chemicals, they may degrade or weaken over time. Inspect regularly and replace if there are signs of chemical damage.
4-2.High Impact or Heavy Use: In environments with frequent high impacts or heavy use, safety glasses may need to be replaced more frequently due to the increased wear and tear.
5.Manufacturer's Recommendations:
5-1.Expiration Date: Some manufacturers provide an expiration date or recommended replacement period for safety glasses. Follow these guidelines to ensure maximum protection.
5-2.Periodic Replacement: Even if there are no visible signs of damage, it’s good practice to replace safety glasses periodically (e.g., every 1-2 years) to ensure ongoing effectiveness and compliance with safety standards.
##Best Practices for Maintenance and Inspection
1.Regular Inspection:
1-1.Inspect safety glasses before each use for any signs of damage or wear. Look for scratches, cracks, loose parts, or worn coatings.
2.Proper Cleaning:
2-1.Clean safety glasses regularly with a soft cloth and appropriate cleaning solution to maintain clear vision and prolong the life of the lenses and coatings. Avoid using abrasive materials or harsh chemicals that can damage the lenses.
3.Storage:
3-1.Store safety glasses in a protective case or designated storage area when not in use to prevent damage. Avoid leaving them in places where they could be exposed to harsh conditions or accidental impact.
4.Training and Awareness:
4-1.Ensure that all users are aware of the importance of maintaining and inspecting their safety glasses. Provide training on proper care and the signs that indicate it’s time for replacement.
Conclusion
While there is no one-size-fits-all answer for how often safety glasses should be replaced, regular inspection, proper maintenance, and adherence to manufacturer recommendations are key to ensuring they provide adequate protection. Replace safety glasses immediately if they show signs of damage, wear, or if they no longer fit properly. Regularly evaluate the condition of your safety glasses to maintain a safe working environment.
Factors Affecting the Lifespan of Welding Lenses
1.Type of Lens:
1-1.Passive Welding Lenses: These are typically made from durable materials like polycarbonate with a fixed shade level. They can last a long time if properly cared for and not exposed to significant damage.。
1-2.Auto-Darkening Welding Lenses: These lenses have electronic components that automatically adjust the shade level based on the light intensity. The lifespan of these lenses can be affected by the durability of the electronics and batteries.
2.Frequency of Use:
2-1.Regular Use: If used frequently, welding lenses will wear out faster due to constant exposure to intense light, heat, and potential physical damage.
2-2.Occasional Use: Lenses used less frequently will generally last longer, as they are not subjected to as much wear and tear.
3.Work Environment:
3-1.Harsh Conditions: Welding in harsh environments with high temperatures, dust, or chemical exposure can shorten the lifespan of welding lenses.
3-2.Controlled Conditions: Welding in a controlled environment with minimal exposure to damaging elements can extend the lifespan of the lenses.
4.Maintenance and Care:
4-1.Proper Cleaning: Regular cleaning with appropriate materials helps maintain lens clarity and prolongs their life. Avoid using abrasive materials or harsh chemicals.
4-2.Storage: Storing welding lenses in a protective case or designated safe area when not in use prevents damage and prolongs their lifespan.
##Signs That Welding Lenses Need Replacement
1.Scratches and Damage:
1-1.Any visible scratches, cracks, or chips on the lenses can impair vision and reduce the effectiveness of the protective coatings. Replace lenses if they show significant damage.
2.Degraded Coatings:
2-1.Over time, anti-scratch, anti-fog, or UV protection coatings can wear off. If you notice peeling or reduced effectiveness of these coatings, it’s time to replace the lenses.
3.Reduced Auto-Darkening Functionality:
3-1.For auto-darkening lenses, if the response time slows down, or if the lenses fail to adjust properly to the welding light, they need to be replaced. This can indicate electronic or battery issues.
4.Fogging:
4-1.Persistent fogging that cannot be resolved through cleaning may indicate that the anti-fog coating has degraded.
5.Distorted Vision:
5-1.If the lenses cause any distortion or discomfort while viewing the welding area, they should be replaced to ensure safety and accuracy.
##Manufacturer's Recommendations
###Always check the manufacturer's guidelines for the expected lifespan of the specific welding lenses you are using. Some manufacturers provide recommendations based on average use and maintenance practices.
##Best Practices for Prolonging the Life of Welding Lenses
1.Regular Cleaning:
1-1.Use a soft, lint-free cloth and appropriate cleaning solutions to clean the lenses. Avoid abrasive materials that can scratch the lenses.
2.Proper Storage:
2-1.Store lenses in a protective case or designated area to avoid accidental damage.
3.Routine Inspection:
3-1.Inspect lenses regularly for any signs of wear, damage, or reduced functionality.
4.Battery Maintenance:
4-1.For auto-darkening lenses, replace batteries as needed and follow manufacturer instructions for battery care to ensure optimal performance.
Conclusion
The lifespan of welding lenses can vary widely based on their type, usage, environment, and care. Regular inspection and proper maintenance are key to ensuring they provide effective protection. Replace welding lenses immediately if they show signs of damage, degraded coatings, or reduced functionality to maintain safety and performance in welding tasks.
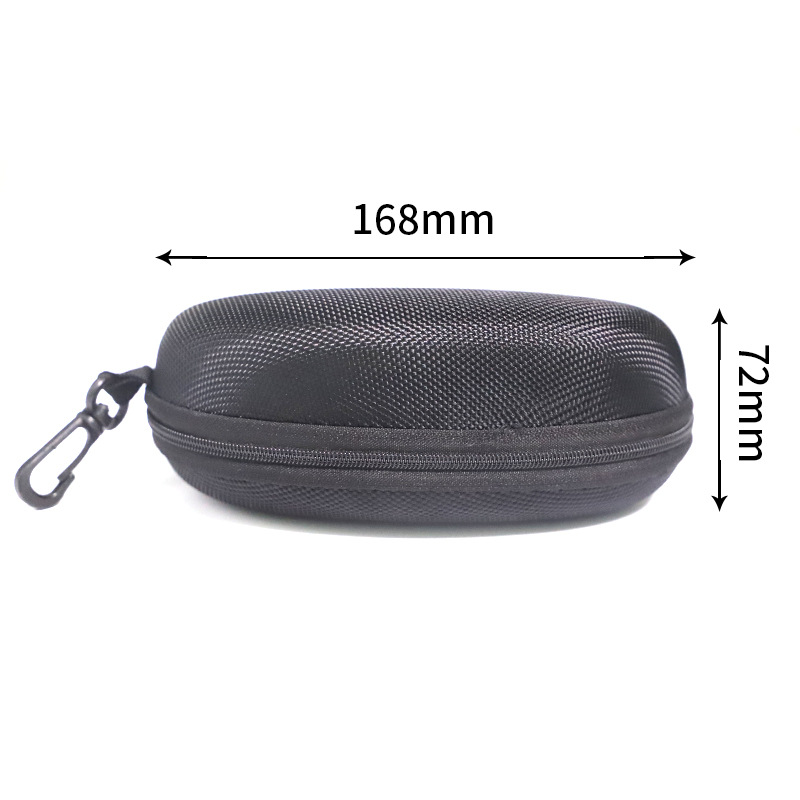
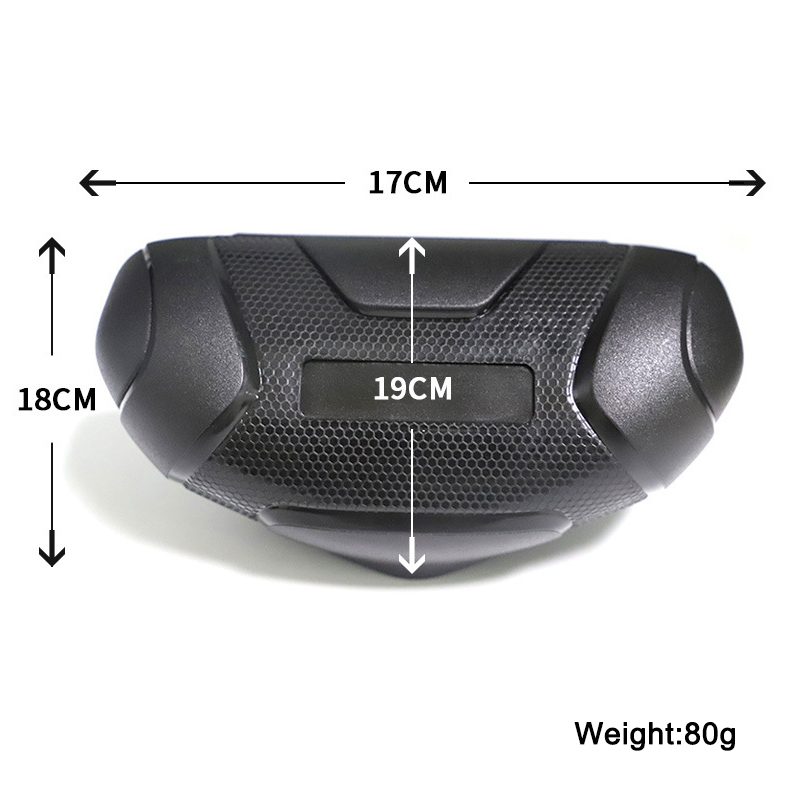
-
Geometric Eyeglasses Frames Retro Round Women T...
-
Factory Wholesale Metal Polygonal Blue Light Gl...
-
Factory Wholesale Metal Tr90 Anti Blue-Ray Eyeg...
-
Blue Light Blocking Glasses for Gaming Women an...
-
Chinese Traditional Wholesale Reading Reading G...
-
Oversize Square Anti blue Light Glasses Frame F...